Hot wire CNC
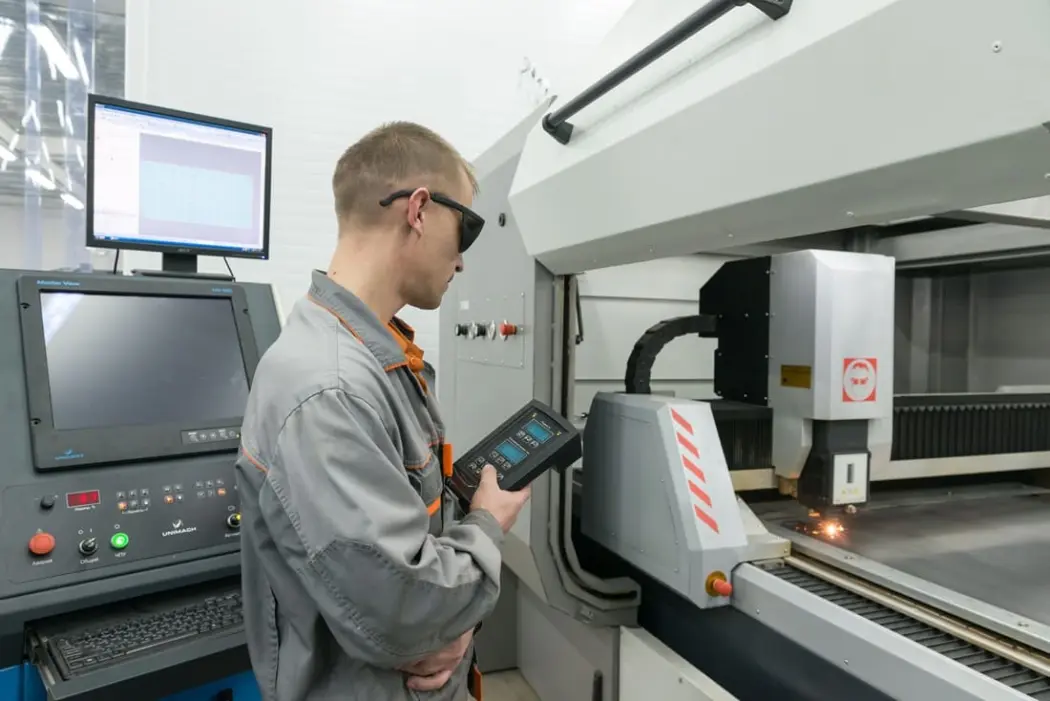
The Hot Wire CNC Foam Cutter is a specialized tool that has revolutionized the way we shape and cut foam. This device uses a heated wire to slice through foam with precision, making it an invaluable asset in industries such as construction, packaging, and even in the arts and crafts sector. The CNC (Computer Numerical Control) aspect of this tool allows for automated control, which means that intricate designs and patterns can be cut with minimal human intervention.
When operating a hot wire CNC Foam Cutter, it’s crucial to follow a specific checklist to ensure optimal performance. First, the design or pattern to be cut is programmed into the CNC system. This can be done using various software applications that are compatible with the machine. Once the design is set, the foam material is placed on the cutting table, and the machine is calibrated to ensure the wire is heated to the right temperature. The cutting process then begins, with the heated wire moving in the pre-programmed pattern, slicing through the foam with ease and precision.
One of the key benefits of using a Hot Wire CNC Foam Cutter is the level of accuracy it provides. Unlike manual cutting methods, this machine can produce consistent results, regardless of the complexity of the design. This is particularly beneficial in industries where precision is paramount. Additionally, because the cutting process is automated, it can save significant time and labor costs. However, it’s important to note that while this machine offers numerous advantages, proper operation and maintenance are essential to ensure its longevity and effectiveness.
In the realm of precision cutting technology, the Hot Wire CNC Foam Cutter has emerged as a game-changer, revolutionizing various industries with its unparalleled functionality and efficiency. As an authority in this field, I am eager to delve into the intricacies of this innovative tool, shedding light on its operation, key features, and the significant role it plays across different sectors.
Hot wire CNC foam cutter
This comprehensive guide will provide an in-depth understanding of the Hot Wire CNC Foam Cutter, equipping you with the knowledge to identify the essential characteristics to consider when investing in this technology. We will also explore its practical application in diverse industries, underscoring its pivotal role in enhancing productivity and precision.
Moreover, we will walk you through the process of operating this tool, ensuring you can utilize its full potential effectively and safely. We will address common troubleshooting issues and provide maintenance tips to extend the lifespan of your equipment. Lastly, we will look ahead to the future of foam cutting technology, exploring the potential advancements that could further transform this field.
Whether you are a seasoned professional or a novice in the world of CNC foam cutting, this article aims to support and guide you in maximizing the benefits of this cutting-edge technology.
Key Features to Look for in a Hot Wire CNC Foam Cutter
When it comes to selecting a high-quality hot wire CNC foam cutter, there are several key features to consider. Accuracy is paramount, as the precision of the cuts can significantly impact the final product. The machine should be able to make precise cuts, even in intricate designs. Additionally, the speed of the machine is another crucial factor. A good foam cutter should be able to maintain its accuracy even at high speeds, allowing for efficient production.
Another important feature to look for is the software compatibility. The machine should be compatible with various design software to allow for flexibility in creating designs. It should also have a user-friendly interface for ease of use. Furthermore, the machine should have a robust construction to ensure durability and longevity. Here are some key features to consider:
- High cutting accuracy
- Fast cutting speed
- Software compatibility
- Robust construction
Lastly, consider the support and warranty provided by the manufacturer. A good manufacturer will provide comprehensive support, including troubleshooting and maintenance. The warranty period should also be reasonable to protect your investment. In conclusion, when choosing a hot wire CNC foam cutter, it’s essential to consider the accuracy, speed, software compatibility, construction, and the support and warranty provided by the manufacturer.
The Role of Hot Wire CNC Foam Cutters in Various Industries
Within a variety of industries, Hot Wire CNC Foam Cutters play a pivotal role in shaping and designing foam materials. These industries range from construction and packaging to arts and crafts, and even the aerospace sector. The precision and efficiency provided by these machines are unparalleled, making them an essential tool in these fields.
Consider the construction industry, for instance. Here, foam is often used for insulation purposes. With the help of a Hot Wire CNC Foam Cutter, large foam blocks can be cut into precise shapes and sizes, ensuring a perfect fit for any construction project. Similarly, in the packaging industry, these machines are used to create custom foam inserts that provide optimal protection for products during transit. The ability to create custom shapes and sizes is a significant advantage, allowing for a more efficient and cost-effective packaging process. Some key benefits include:
- High precision cutting: Ensures accurate shapes and sizes every time.
- Customization: Allows for the creation of unique designs tailored to specific needs.
- Efficiency: Speeds up the production process, saving time and resources.
Furthermore, in the arts and crafts sector, Hot Wire CNC Foam Cutters are used to create intricate designs and sculptures. The machine’s ability to cut foam with such precision opens up a world of possibilities for artists and crafters. In the aerospace industry, these cutters are used to create lightweight yet sturdy components. The versatility and precision of Hot Wire CNC Foam Cutters make them an invaluable tool in these and many other industries.
Step-by-Step Guide to Operating a Hot Wire CNC Foam Cutter
Operating a hot wire CNC foam cutter can seem daunting at first, but with a systematic approach, it becomes quite manageable. Understanding the process is key to achieving the best results. Here’s a step-by-step guide to help you navigate through the operation:
- Prepare your design: Start by creating a digital design of the object you want to cut. This can be done using CAD software.
- Set up the machine: Ensure that the hot wire is correctly installed and the machine is properly calibrated.
- Load the design: Import your design into the CNC software. Make sure to adjust the settings according to the foam material you are using.
- Start the cutting process: Once everything is set, initiate the cutting process. Monitor the machine closely to ensure everything goes as planned.
- Post-processing: After the cutting is complete, remove any excess material and smooth out the edges if necessary.
Remember, safety should always be your top priority when operating a hot wire CNC foam cutter. Always wear protective gear and follow the manufacturer’s instructions.
Safety Measures to Consider When Using a Hot Wire CNC Foam Cutter
Ensuring safety while operating machinery is paramount, and a Hot Wire CNC Foam Cutter is no exception. It is crucial to understand the potential hazards associated with this tool and take necessary precautions to avoid accidents. One of the primary safety measures is to always wear protective gear. This includes safety glasses to protect your eyes from any flying debris, gloves to shield your hands from heat, and a dust mask to prevent inhalation of foam particles. Furthermore, it is advisable to work in a well-ventilated area to avoid the accumulation of harmful fumes.
Another significant safety measure is proper handling and maintenance of the machine. Regular inspection of the hot wire is essential to ensure it is not frayed or damaged, as this could lead to electrical shocks or fires. Additionally, the workspace should be kept clean and free from flammable materials. It is also important to remember to turn off and unplug the machine when not in use or during maintenance. Lastly, while the machine’s operation may seem straightforward, it is always safer to undergo proper training or refer to the user manual before using the Hot Wire CNC Foam Cutter.
Troubleshooting Common Issues with Hot Wire CNC Foam Cutters
Experiencing issues with your hot wire CNC foam cutter can be frustrating, especially when you’re in the middle of a project. However, most problems are common and can be easily fixed with a little knowledge and patience. One common issue is the wire not heating up. This could be due to a faulty power supply, a broken wire, or an issue with the temperature control. Always check these components first if your wire isn’t heating up. Tip sheets provided by the manufacturer can be a great resource for troubleshooting these issues.
Another common problem is the foam not cutting cleanly or accurately. This could be due to a number of factors, including the wire tension, the speed of the cut, or the type of foam being used. Adjusting the wire tension and cut speed can often resolve these issues. If you’re still having trouble, it may be worth trying a different type of foam. Remember, consulting the tip sheets or user manual can provide valuable guidance for these adjustments.
Maintenance Tips for Prolonging the Life of Your Hot Wire CNC Foam Cutter
Regular upkeep of your equipment is crucial to ensure its longevity. Proper maintenance of your hot wire CNC foam cutter not only enhances its performance but also extends its lifespan. It’s essential to keep the machine clean, especially the cutting wire and the working table. Accumulated foam residue can affect the cutting precision and overall performance of the machine. Therefore, cleaning after each use is a must. Also, regular inspection of the wire tension is necessary. An undefined or loose wire can lead to inaccurate cuts and potential damage to the machine.
Another vital aspect of maintenance is the regular lubrication of moving parts. This reduces friction and prevents wear and tear, thus prolonging the machine’s life. Additionally, it’s important to ensure that the machine’s software is always up to date. Software updates often include performance improvements and bug fixes that can enhance the machine’s efficiency. Lastly, always follow the manufacturer’s guidelines for maintenance and service. This will help you avoid any unnecessary damage and ensure that your hot wire CNC foam cutter remains in top condition.
Exploring the Future of Hot Wire CNC Foam Cutting Technology
As we delve deeper into the 21st century, the advancements in Hot Wire CNC Foam Cutting Technology are becoming increasingly impressive. With the rise of automation and precision engineering, this technology is set to revolutionize various industries, including construction, packaging, and aerospace. The future holds a plethora of possibilities, with the potential for even more efficient and accurate cutting processes. The key to unlocking these advancements lies in continuous research and development, as well as the integration of advanced software and hardware components.
Looking ahead, there are several areas of focus that could significantly enhance the capabilities of hot wire CNC foam cutters. Artificial Intelligence (AI) and Machine Learning (ML) are two such areas. By incorporating these technologies, we could see machines that learn from their mistakes, adapt to different foam types, and optimize their cutting paths for maximum efficiency. Furthermore, the advent of Internet of Things (IoT) could allow for remote operation and real-time monitoring of these machines. Here’s a quick checklist for the future advancements to look out for:
- Integration of AI and ML for smarter operation
- Use of IoT for remote control and monitoring
- Development of advanced software for improved precision
- Research into new materials for enhanced durability
quently Asked Questions
What materials can be cut with a Hot Wire CNC Foam Cutter?
Hot Wire CNC Foam Cutters are primarily designed to cut foam materials. However, they can also cut other materials that melt easily, such as polystyrene, polyethylene, and certain types of plastic. It’s important to check the manufacturer’s guidelines for the specific materials your machine can handle.
How precise is the cutting process with a Hot Wire CNC Foam Cutter?
The precision of a Hot Wire CNC Foam Cutter is one of its key advantages. These machines can cut with a precision of up to 0.5mm, making them ideal for intricate designs and detailed work. However, the exact precision can vary depending on the specific model and settings used.
Can a Hot Wire CNC Foam Cutter be used for large-scale production?
Yes, Hot Wire CNC Foam Cutters are suitable for both small-scale and large-scale production. They are commonly used in industries such as construction, packaging, and aerospace for mass production. The speed and efficiency of the cutting process can be adjusted to meet the demands of large-scale production.
What is the lifespan of a Hot Wire in a CNC Foam Cutter?
The lifespan of a hot wire in a CNC foam cutter can vary greatly depending on usage and maintenance. With regular use and proper care, a hot wire can last for several months. However, it’s recommended to have replacement wires on hand as they can break or wear out over time.
Is special training required to operate a Hot Wire CNC Foam Cutter?
While operating a Hot Wire CNC Foam Cutter does require knowledge of CNC operations and safety measures, it doesn’t necessarily require special training. Most manufacturers provide detailed user manuals and some even offer training sessions. However, for complex projects or industrial applications, professional training might be beneficial.
Autor: Materiał partnera